How to Troubleshoot Electrical Problems in Diesel-Powered Hay Balers
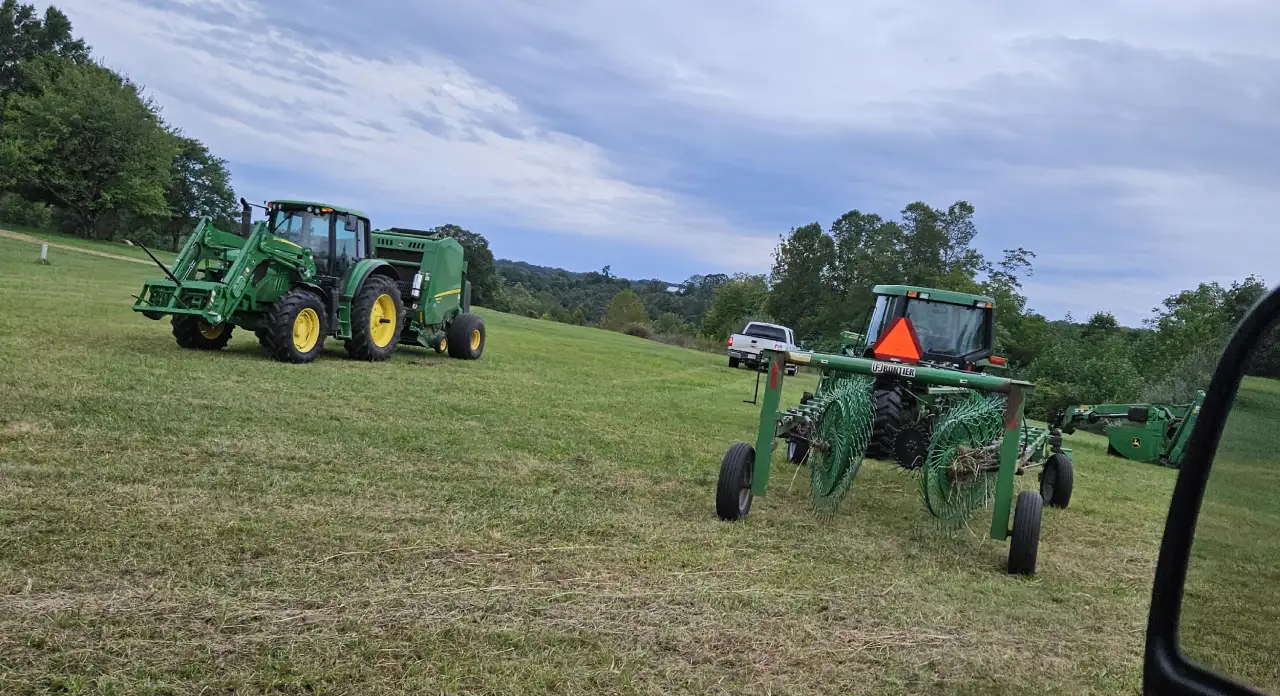
Diesel-powered hay balers are workhorses on the farm, converting raw hay into bales efficiently. However, like any machinery, they aren't immune to electrical issues. Given the complexity of diesel engines and balers' electrical systems, diagnosing and resolving these problems can be daunting. Here's a guide to help you navigate common electrical issues in diesel-powered hay balers, ensuring your machine keeps churning out bales with minimal downtime.
Common Electrical Problems in Diesel Hay Balers
The electrical system of a diesel-powered hay baler is composed of many components—battery, alternator, starter motor, wiring, relays, and control modules. Issues with any of these can halt operations. Let's look at some of the most prevalent electrical problems you might encounter.
Battery Issues
First off, a bad battery is one of the most common culprits. Diesel hay balers rely heavily on the battery to start the engine and power electrical components, like sensors and control panels. Symptoms of battery issues include:
- Weak cranking or failure to start
- Dimming lights or flickering display panels
- Frequent need for a jump start
Troubleshooting Tip: Start by testing the battery's voltage using a multimeter. When fully charged, it should read between 12.6V and 13.2V. If the voltage is low, try charging the battery. If charging doesn’t work, you may need to replace it. Ensure the terminals are clean and corrosion-free; dirty or loose connections can mimic battery failure symptoms.
Alternator Problems
An alternator supplies power to the baler's electrical system while the engine runs. It also charges the battery. When the alternator malfunctions, you may notice the following:
- Dim or flickering lights while operating the baler
- The battery frequently drains
- Warning lights on the control panel
Troubleshooting Tip: Check the alternator belt for tension and wear; a loose or broken belt can prevent the alternator from generating power. If the belt looks fine, measure the alternator output. When the engine is running, it should read between 13.5V and 14.5V. If it falls outside this range, the alternator may need replacement.
Starter Motor Failure
The starter motor is responsible for cranking the engine. A failing starter motor can prevent the baler from starting altogether. Signs of starter motor issues include:
- A clicking sound when you turn the key
- The engine fails to crank or cranks very slowly
- Intermittent starting issues
Troubleshooting Tip: Begin by checking the starter relay and solenoid. If it functions correctly, test the starter motor by connecting it directly to the battery with jumper cables. If the motor doesn't spin, it's likely failed and needs replacement.
Wiring and Connections
With balers working in dusty, dirty environments, wiring issues are too common. Loose, frayed, or corroded wires can wreak havoc on the machine's electrical system. Key areas to inspect include:
- Battery terminals
- Ground connections
- Wires running to the sensors, control panels, and switches
Troubleshooting Tip: If you notice any signs of damaged wiring—like fraying, corrosion, or burn marks—replace the wire immediately. Check all connections for tightness, especially grounds, as poor grounding can lead to erratic behavior.
Sensor Malfunctions
Modern diesel hay balers rely on various sensors to monitor the machine's performance, such as pressure, RPM, and temperature sensors. When one of these sensors fails, it can disrupt normal operation, sometimes causing the baler to shut down completely.
Troubleshooting Tip: Utilize the onboard diagnostic system (if equipped) to retrieve any fault codes. These codes can direct you to the problematic sensor. If a sensor is flagged, inspect its wiring and replace it if necessary.
Preventive Maintenance for Electrical Systems
Regular preventive maintenance is critical to minimizing the risk of electrical problems on your hay baler. This includes:
- Inspecting and cleaning battery terminals regularly
- Checking the alternator belt for signs of wear
- Ensuring wiring and connections are properly secured and free of debris
- Testing the battery with a multimeter periodically to check its health
- Recharging or replacing batteries that show signs of weakness
By performing these routine checks, you can catch minor problems before they escalate into significant issues, helping to ensure that your baler remains operational during the busiest seasons.
Conclusion
Electrical issues can be frustrating, but with some patience and troubleshooting, most problems on diesel-powered hay balers can be solved. Regularly maintaining your baler’s electrical components and promptly addressing any symptoms can reduce downtime and keep your equipment running smoothly. Battery, alternator, and starter motor issues are among the most common problems, so start there. Ensure all wiring is clean and tightly connected to prevent intermittent faults.
Do you have any questions or need help with diesel repairs? Feel free to contact us—we’re always here to assist with your heavy-duty machinery needs.